BLOG
OEM Power Supply Manufacturing: How AI, Robotics, and Smart Technology Are Transforming the Industry
Table of contents
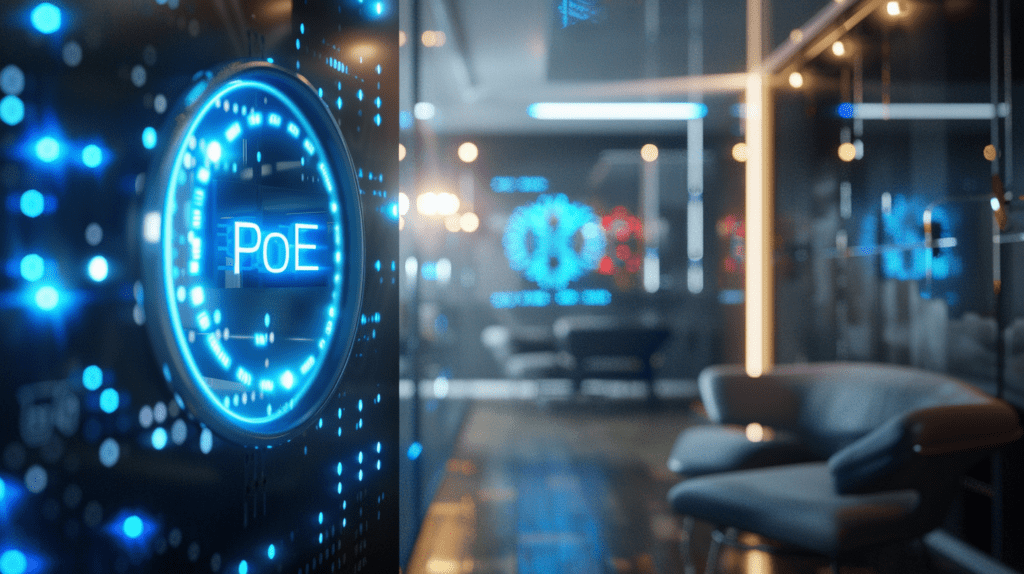
As industries evolve, OEM power supply manufacturers are embracing new technologies to meet the increasing demands of efficiency, automation, and sustainability. The future of power supply manufacturing is being shaped by AI-driven smart power management, robotics in production, and advancements in energy-efficient designs.
From self-regulating power systems for medical devices to robotic assembly lines that improve precision and scalability, decision-makers must stay ahead of these emerging trends. This article explores the future of OEM power supply manufacturing, highlighting the innovations that will define next-generation power solutions.
AI-Powered Smart Power Supplies: The Rise of Intelligent Energy Management
Artificial Intelligence (AI) is revolutionizing power supply technology by enabling real-time power monitoring, adaptive energy distribution, and predictive maintenance. AI-driven smart power supplies can automatically adjust voltage, optimize energy usage, and detect potential failures before they occur.
Key Innovations in AI-Driven Power Supply Design
- Self-learning power regulation – AI algorithms analyze power consumption patterns and adjust voltage levels accordingly to reduce waste and maximize efficiency.
- Predictive maintenance and remote monitoring – AI-powered power supplies can detect and prevent faults, minimizing downtime and ensuring continuous operation for critical systems.
- Grid-connected smart power systems – AI optimizes load balancing for renewable energy sources, enhancing battery storage performance and sustainable power integration.
Best Practices for OEMs Adopting AI-Enhanced Power Supplies
- Partner with power supply manufacturers that integrate AI-driven energy analytics into their designs.
- Invest in smart monitoring solutions that provide real-time diagnostics and automated performance tuning.
- Ensure AI-powered power systems comply with ISO 50001 (Energy Management) and IEC safety regulations for safe implementation.
AI-powered power supplies will become the new standard for automated medical devices, industrial automation, and next-gen IoT-connected systems, ensuring maximum efficiency and reliability.
Robotics in OEM Power Supply Manufacturing: Precision, Scalability, and Automation
The integration of robotics in OEM power supply production is transforming manufacturing speed, quality, and scalability. Robotics is enabling automated circuit board assembly, high-precision component soldering, and real-time quality control, reducing human error and improving production efficiency.
How Robotics is Reshaping Power Supply Manufacturing
- Automated PCB assembly – Robotic precision ensures flawless soldering, wire bonding, and component placement, minimizing defects in power supply circuits.
- AI-guided quality inspections – Machine learning algorithms scan PCBs for imperfections in real time, reducing the need for manual inspection.
- Scalable and flexible production lines – Robotic systems allow for rapid production adjustments, supporting both high-volume manufacturing and low-batch prototyping.
Best Practices for OEMs Implementing Robotics in Manufacturing
- Work with manufacturers that have fully automated production lines for consistent quality control.
- Ensure that robotics-enabled power supply assembly complies with IPC-A-610 electronic manufacturing standards.
- Utilize collaborative robots (cobots) for flexible manufacturing solutions that enhance workforce productivity.
With robotic automation, OEMs can achieve greater production consistency, reduced manufacturing costs, and improved scalability, positioning themselves for the future of high-tech power supply production.
Next-Generation Energy Efficiency: The Future of High-Performance Power Supply Design
As industries move toward carbon neutrality and sustainability, power supply manufacturers are developing ultra-efficient designs that minimize energy waste. Future power supply innovations will incorporate advanced semiconductors, zero-standby power technology, and ultra-low-loss components to meet strict global efficiency regulations.
Emerging Trends in Power Efficiency
- Gallium Nitride (GaN) and Silicon Carbide (SiC) semiconductors – These materials allow for higher switching frequencies, reduced thermal losses, and smaller form factors in power supplies.
- Zero-standby power technology – Future power supplies will eliminate idle power consumption, complying with DOE Level VI and EU CoC Tier 3 energy efficiency mandates.
- Solid-state batteries and supercapacitors – Innovations in energy storage will enable power supplies with ultra-fast charging and extended backup capabilities.
Best Practices for OEMs Looking to Future-Proof Their Power Supplies
- Choose manufacturers investing in GaN and SiC-based power solutions to improve efficiency.
- Ensure compliance with international energy efficiency standards to future-proof products.
- Integrate intelligent power management software to track and optimize energy consumption.
By adopting high-efficiency power technologies, OEMs can reduce operational costs, minimize carbon footprints, and stay ahead of evolving industry regulations.
The Role of IoT-Connected Power Supplies in Future OEM Applications
The Internet of Things (IoT) is revolutionizing power supply management, enabling real-time monitoring, cloud-based analytics, and automated system updates. IoT-connected power supplies will drive higher intelligence, security, and integration across multiple industries, from healthcare and smart factories to autonomous robotics.
How IoT-Enabled Power Supplies Will Transform OEM Manufacturing
- Remote diagnostics and predictive maintenance – IoT sensors detect power anomalies and overheating risks, sending alerts to prevent system failures.
- Cloud-based firmware updates – Future power supplies will be able to receive security patches and efficiency improvements over the air, reducing downtime.
- Adaptive power distribution – IoT-based power systems will dynamically adjust voltage and current outputs based on real-time device requirements.
Best Practices for Implementing IoT in Power Supply Design
- Select manufacturers that offer IoT-enabled power management solutions for real-time monitoring.
- Ensure IoT security features comply with IEC 62443 (Cybersecurity for Industrial Automation) to protect against cyber threats.
- Invest in cloud-based diagnostics and analytics platforms to optimize power system performance.
With IoT-powered smart energy management, OEMs can create self-regulating power systems that improve operational efficiency, predictive maintenance, and energy sustainability.
CLIENT'S QUOTE
"Phihong’s PoE solutions have made a huge difference for us! Our network runs more efficiently, and we’ve seen real cost savings. We couldn’t be happier!"
Sustainable Manufacturing and Eco-Friendly Power Supply Solutions
As global industries prioritize sustainability and energy efficiency, OEM power supply manufacturers are shifting toward eco-friendly production methods and recyclable materials. The future of power supply manufacturing involves reducing carbon footprints, minimizing waste, and adopting greener energy solutions while maintaining high-performance power conversion.
Key Innovations in Sustainable Power Supply Manufacturing
- Use of recyclable and lead-free components – Manufacturers are phasing out hazardous materials like lead, mercury, and cadmium, adhering to RoHS and WEEE compliance.
- Renewable energy integration – Future factories will rely more on solar, wind, and hydroelectric power sources to manufacture power supplies sustainably.
- Ultra-efficient power designs – Next-gen GaN (Gallium Nitride) and SiC (Silicon Carbide) semiconductors provide higher power density while reducing heat waste.
Best Practices for OEMs Seeking Sustainable Power Solutions
- Choose power supply manufacturers that incorporate energy-efficient designs and recyclable materials.
- Ensure compliance with eco-friendly regulations like RoHS, WEEE, and Energy Star certifications.
- Work with suppliers implementing carbon-neutral and waste-reduction manufacturing processes.
By adopting sustainable manufacturing practices, OEMs can reduce environmental impact, improve efficiency, and align with global energy regulations, making their power solutions future-proof and environmentally responsible.
Autonomous Quality Control: AI-Driven Testing and Precision Manufacturing
AI and machine learning are revolutionizing quality control in OEM power supply manufacturing, enabling real-time defect detection, automated performance testing, and predictive maintenance. These advancements ensure that power supplies meet strict compliance and safety standards while reducing errors and production costs.
How AI-Powered Quality Control Improves Power Supply Manufacturing
- Real-time defect detection – Machine vision and AI-powered analytics identify micro-level inconsistencies in circuit board production, ensuring higher reliability.
- Automated electrical safety testing – AI-based stress tests, voltage regulation analysis, and efficiency modeling guarantee compliance with IEC, UL, and ISO standards.
- Self-learning inspection systems – AI-driven quality control continuously improves accuracy and consistency in power supply production.
Best Practices for OEMs Adopting AI in Manufacturing
- Partner with manufacturers that leverage AI-powered defect detection for enhanced production accuracy.
- Ensure AI-driven testing validates compliance with international safety and efficiency regulations.
- Invest in predictive maintenance AI tools that monitor power supply performance and detect faults before they occur.
By integrating AI into quality control, OEM manufacturers can increase precision, reduce material waste, and produce safer, more efficient power supplies.
Phihong: Leading the Future of OEM Power Supply Manufacturing
As OEMs navigate the future of power supply technology, working with a trusted and innovative manufacturer is essential for staying ahead in a competitive landscape. Phihong is at the forefront of AI-powered power solutions, robotic manufacturing, and next-generation energy efficiency, delivering high-performance OEM power supplies for industries such as medical, industrial automation, and telecommunications.
Why Choose Phihong?
- AI-driven smart power solutions – Phihong integrates real-time diagnostics and predictive analytics into power supply designs.
- Fully automated manufacturing – Robotic assembly lines ensure precision, scalability, and quality control.
- Next-gen energy efficiency and GaN-based designs – High-efficiency power supplies with ultra-low power consumption and eco-friendly materials.
- IoT-enabled power systems – Cloud-based monitoring, adaptive power distribution, and remote updates.
- Global manufacturing in Vietnam – Reliable production with fast lead times and flexible supply chain solutions.
With a commitment to technological advancement, regulatory compliance, and customized OEM solutions, Phihong is the go-to partner for future-proof power supply innovations.
Partner with Phihong today to power the future of your OEM solutions.
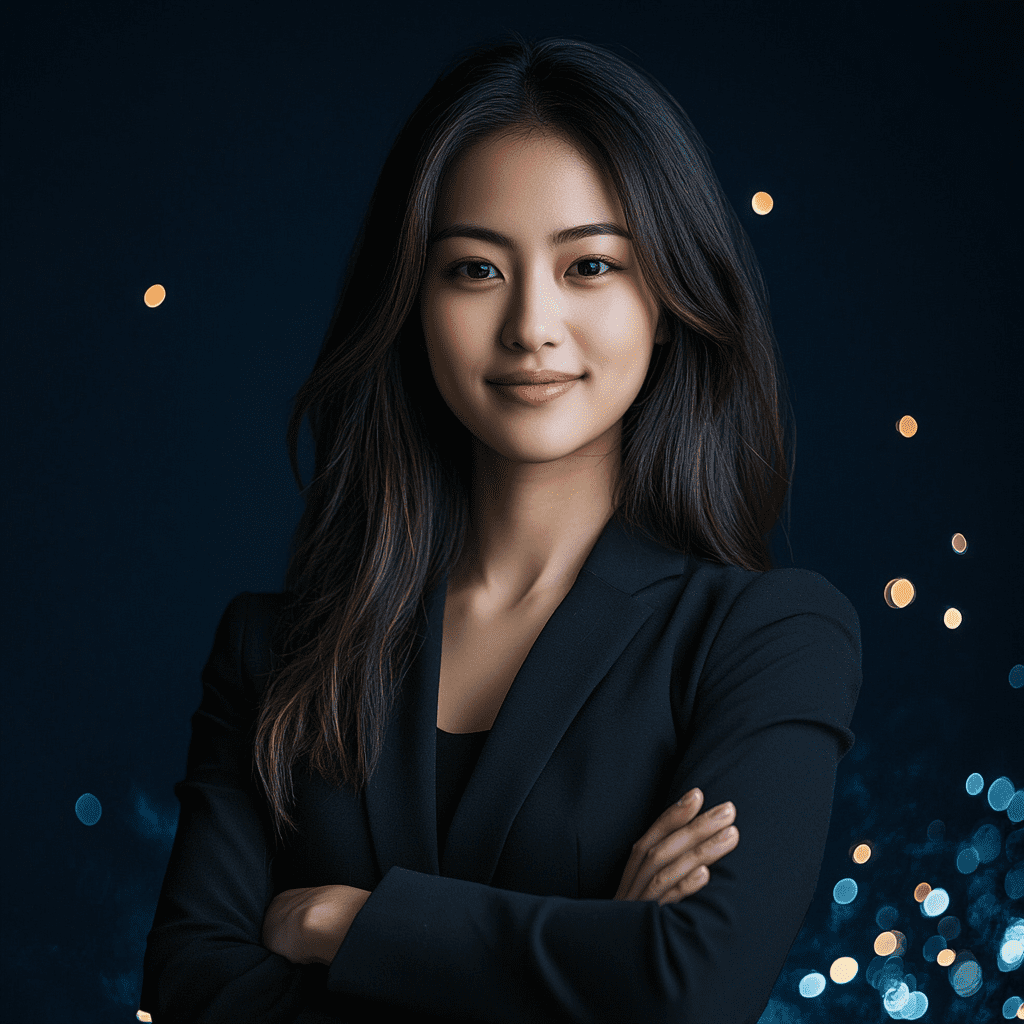
Contact Our Team Today!
Our dedicated sales team and international partners are prepared to support you with your latest projects and initiatives globally.
Explore More with Phihong USA
As we conclude our exploration of PoE technology, it’s evident how these innovations are streamlining power and data integration across various industries. Phihong USA stands at the forefront of this technological advancement, offering a diverse range of power solutions designed to meet the evolving needs of modern industries.
Phihong USA’s extensive product lineup includes:
- Power over Ethernet (PoE) Solutions: Delivering reliable power and data transmission over a single cable, ideal for simplifying network installations and reducing costs.
- AC/DC Adapters and Power Supplies: From compact adapters to industrial-grade power supplies, Phihong provides solutions that ensure efficiency and reliability in various applications.
- Battery Chargers: Customizable chargers for lithium-ion and lead-acid batteries, supporting a wide range of power requirements for mobility and industrial applications.
- Medical Power Supplies: Specialized power solutions designed to meet the stringent requirements of the healthcare industry, ensuring safety and reliability.
Phihong USA is committed to innovation and excellence, continually developing products that meet the highest standards of performance and reliability. Their global reach and dedication to customer support make them a trusted partner in powering the future.
Here are some useful links to explore Phihong USA’s offerings further and bring in new potential clients:
Visit Phihong USA to discover how their advanced power solutions can support your business needs. Whether you’re looking to upgrade your network, or find reliable power supplies, Phihong USA has you covered.
By choosing Phihong USA, you’re partnering with a leader in power technology, ensuring your operations run smoothly and efficiently with top-tier power solutions. Contact Us today!
FAQ
How will AI impact the future of OEM power supply manufacturing?
AI will revolutionize OEM power supply manufacturing by enabling predictive maintenance, automated quality control, and smart energy management. AI-powered algorithms will allow manufacturers to detect power inefficiencies, predict failures, and dynamically adjust voltage outputs based on real-time power consumption analytics.
AI-driven robotic testing and defect detection will also improve manufacturing precision, ensuring that every power supply unit meets strict industry standards. This automation reduces human error, speeds up production, and enhances power system reliability, making AI one of the most transformative forces in power supply manufacturing.
Additionally, AI-integrated power supplies will support IoT-enabled devices, allowing medical, industrial, and telecom applications to remotely monitor energy usage, optimize load balancing, and automate power distribution.
By investing in AI-enhanced power supply technology, OEMs can increase operational efficiency, reduce costs, and develop smarter, more adaptable power solutions.
What role does robotics play in modern power supply manufacturing?
Robotic automation is enhancing speed, precision, and scalability in OEM power supply manufacturing. Automated PCB assembly lines and robotic soldering systems enable high-precision circuit production, reducing defects and increasing production output.
Robotic vision systems and AI-guided quality control further ensure that each power supply unit is tested to the highest safety and efficiency standards. Robotics also play a role in automated testing of voltage stability, thermal efficiency, and durability, allowing manufacturers to meet international compliance requirements more efficiently.
For OEMs, the adoption of robotics in power supply manufacturing translates to consistent product quality, faster production cycles, and lower overall costs, making it a key driver of future industry growth.
How will sustainable manufacturing impact the future of power supplies?
Sustainable manufacturing will shape the future of OEM power supply production by reducing carbon emissions, optimizing energy efficiency, and using environmentally friendly materials.
New lead-free, RoHS-compliant designs ensure that power supplies are safer for the environment while meeting global energy efficiency regulations like DOE Level VI and EU CoC Tier 3. Manufacturers are also integrating renewable energy sources into production facilities to further reduce emissions and lower energy consumption.
Additionally, advances in solid-state batteries and energy-efficient GaN-based power supplies will allow future power supply designs to use less raw material while increasing output efficiency, ensuring OEMs remain compliant with future sustainability regulations.
How will IoT improve power supply technology in the coming years?
IoT-enabled power supplies will enable real-time energy monitoring, predictive analytics, and cloud-based firmware updates. These innovations will allow remote diagnostics, self-regulating voltage control, and automated system optimization, improving energy efficiency and device longevity.
IoT-based smart grid integration will also enable adaptive power distribution for industrial automation, medical applications, and telecom networks, optimizing power delivery while reducing operational costs.
For OEMs, the integration of IoT technology in power supplies means greater control over energy usage, better predictive maintenance, and enhanced safety for mission-critical applications.
Why should OEMs choose Phihong as their future-ready power supply partner?
Phihong is a leading innovator in OEM power supply manufacturing, offering customized, high-efficiency power solutions with AI-powered diagnostics, robotic precision assembly, and sustainable manufacturing practices.
Key Advantages of Phihong’s OEM Power Solutions:
- AI-driven smart energy management – Predictive power control and real-time monitoring.
- Robotic automation – Ultra-precise circuit manufacturing and defect reduction.
- Eco-friendly designs – Energy-efficient power supply solutions that meet global sustainability standards.
- Scalable, high-performance OEM power solutions – Designed for medical, industrial, and telecom applications.
- Reliable supply chain management – Global manufacturing hubs in Vietnam ensure fast production and consistent availability.
As the industry evolves, OEMs need a partner who embraces next-generation power solutions, and Phihong is leading the way in future-ready, AI-enhanced, and IoT-integrated power supply manufacturing.
Partner with Phihong today to power the future of your OEM solutions.