BLOG
Top 10 Key Considerations for OEM Manufacturers When Choosing a Custom Power Supply Partner
Table of contents
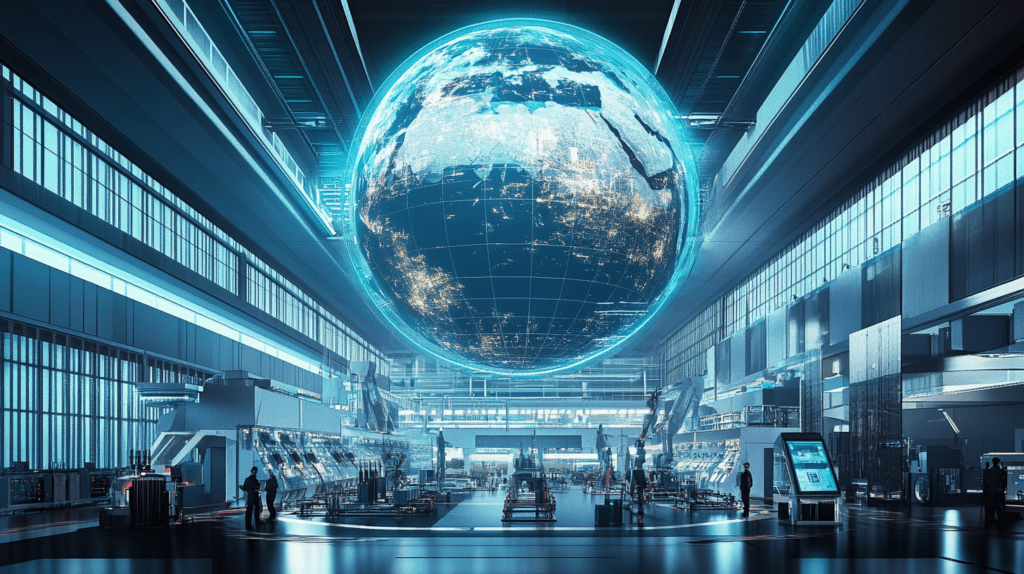
Selecting the right custom power supply partner is a crucial decision for OEM manufacturers who require high-efficiency, reliable, and compliant power solutions. Whether you operate in industrial automation, medical devices, telecommunications, or automotive electronics, choosing a trusted power supply manufacturer impacts the performance, safety, and longevity of your products.
A reliable OEM power supply manufacturer should offer customized solutions tailored to your voltage, efficiency, and form factor requirements while meeting strict regulatory standards. This article outlines the top 10 considerations OEMs must evaluate when selecting a custom power supply partner, ensuring long-term reliability and seamless integration into your product line.
1. Engineering and Design Expertise in Custom Power Solutions
The foundation of a high-quality custom power supply is engineering expertise. OEM manufacturers must assess whether their power supply partner has the technical knowledge and experience to design, prototype, and manufacture high-efficiency power solutions that meet industry demands.
Key Considerations
- Do they have in-house engineers who can design custom PCB layouts, thermal management solutions, and high-efficiency power circuits?
- Can they offer rapid prototyping and custom firmware modifications to meet your product’s specific needs?
- Do they support wide input voltage ranges, high-efficiency conversion, and power factor correction (PFC) for global applications?
Key Features and Benefits
- Optimized power efficiency – Reduces energy consumption and heat dissipation.
- Tailored voltage regulation – Ensures seamless integration with OEM devices.
- Thermal management solutions – Extends product lifespan and improves reliability.
Best Practices
- Work with a manufacturer that provides end-to-end engineering support, from concept to final production.
- Request prototype samples to evaluate the performance and efficiency of their designs.
- Ensure their engineering team can customize power solutions for unique applications in your industry.
Partnering with an experienced custom power supply manufacturer ensures high-quality, reliable, and optimized solutions for your OEM products.
2. Compliance with Industry Certifications and Safety Standards
Regulatory compliance is non-negotiable for OEM manufacturers, especially in medical, industrial, and telecom applications where power failures or electrical faults could lead to serious risks. Your power supply partner should have the necessary certifications to meet international safety, environmental, and performance standards.
Essential Certifications to Look For
Certification | Industry | Purpose |
UL 62368-1 | IT and Telecom | Ensures safe operation of electronic equipment. |
IEC 60601 | Medical Devices | Required for patient-connected medical equipment. |
ISO 9001 | General | Guarantees quality management and consistent production. |
MIL-STD-810 | Defense and Aerospace | Governs ruggedized electronics for harsh environments. |
RoHS & WEEE | Environmental | Ensures compliance with hazardous material and disposal regulations. |
Key Features and Benefits
- Regulatory compliance – Reduces the risk of non-compliance penalties or recalls.
- Improved safety and reliability – Ensures power supplies meet industry-mandated safety standards.
- Global market approval – Enables faster product deployment in multiple regions.
Best Practices
- Work with a manufacturer that actively updates their certifications to comply with evolving regulations.
- Ensure they conduct electromagnetic compatibility (EMC) and electrical safety tests before product deployment.
- Request third-party certification reports to verify compliance with industry standards.
Ensuring certification compliance guarantees that your OEM power supply meets safety, efficiency, and environmental regulations worldwide.
3. Scalability and Manufacturing Capabilities
As an OEM manufacturer, your power supply requirements may evolve over time. Your power supply partner should have scalable production capabilities to support small-batch prototyping, mid-scale production, and high-volume manufacturing without compromising quality or consistency.
Key Considerations
- Do they offer low-MOQ (Minimum Order Quantity) production for initial testing?
- Can they ramp up to mass production while maintaining lead times?
- Do they have multiple manufacturing locations to ensure supply chain stability?
Key Features and Benefits
- Production scalability – Supports growth without production delays.
- Flexible manufacturing – Accommodates custom designs and product iterations.
- Supply chain resilience – Ensures continuous product availability even during component shortages.
Best Practices
- Partner with a manufacturer that offers customized supply chain solutions, including JIT (Just-In-Time) inventory management.
- Evaluate their ability to source high-quality components while minimizing lead times.
- Ensure they have contingency plans for global supply chain disruptions.
Working with a scalable power supply manufacturer helps future-proof your production strategy, ensuring cost-effective expansion as your product demand grows.
4. Longevity, Lifecycle Support, and Reliability
The longevity of a custom power supply directly impacts the total cost of ownership (TCO) and operational reliability of your products. Choosing a power supply partner that offers long-term support, firmware updates, and post-production assistance is critical for maintaining performance over time.
Key Considerations
- Does the manufacturer offer firmware updates and efficiency upgrades?
- Can they provide field service support for troubleshooting or repairs?
- Do they have a proven track record of producing high-MTBF (Mean Time Between Failures) power supplies?
Key Features and Benefits
- Extended product lifespan – Reduces downtime and maintenance costs.
- Post-production support – Provides long-term assistance for firmware improvements and hardware modifications.
- Future scalability – Allows seamless integration with next-generation devices.
Best Practices
- Choose a manufacturer that guarantees component availability for at least 5-10 years to avoid early product obsolescence.
- Request environmental testing reports to ensure durability under real-world conditions.
- Partner with companies that provide structured product lifecycle management (PLM) to track performance and upgrades.
Ensuring long-term reliability and lifecycle support is essential for OEM manufacturers looking to develop future-proof power solutions.
5. Customization Capabilities and Design Flexibility
OEM manufacturers often require custom power supply designs to fit specific voltage requirements, form factors, and efficiency goals. A reliable power supply partner should offer custom engineering solutions that align with your product design and industry standards.
Key Considerations
- Can the manufacturer provide custom PCB layouts, enclosure modifications, and connector types to meet your device specifications?
- Do they offer programmable power supplies that allow for adjustable voltage and current settings?
- Can they design ruggedized or waterproof enclosures for applications requiring extreme durability?
Key Features and Benefits
- Tailored power solutions – Ensures compatibility with your unique product designs.
- Reduced failure rates – Optimized designs enhance efficiency and reliability.
- Seamless integration – Custom footprints fit space-constrained or modular designs.
Best Practices
- Choose a manufacturer that offers fully customizable power solutions, from output voltage adjustments to housing materials.
- Work closely with their engineering team to define customization parameters that align with your product roadmap.
- Request prototyping and testing services before full-scale production to ensure proper integration with your OEM product.
A power supply partner with strong customization capabilities helps OEMs design high-performance, efficient, and application-specific power solutions.
CLIENT'S QUOTE
"Phihong’s PoE solutions have made a huge difference for us! Our network runs more efficiently, and we’ve seen real cost savings. We couldn’t be happier!"
6. Advanced Power Management and Efficiency Standards
With increasing energy regulations and sustainability concerns, OEMs must ensure their power supplies comply with global efficiency standards. High-efficiency power supplies reduce energy consumption, minimize heat generation, and extend product lifespan.
Key Considerations
- Does the manufacturer offer high-efficiency power designs that meet 80 PLUS®, DOE Level VI, or EU CoC Tier 2 compliance?
- Do they integrate active power factor correction (PFC) to optimize energy use and reduce losses?
- Can they provide smart power monitoring features, such as IoT-enabled energy tracking or remote diagnostics?
Key Features and Benefits
- Lower energy costs – High-efficiency designs reduce waste and heat output.
- Regulatory compliance – Meets global efficiency and sustainability requirements.
- Improved performance – Enhances device operation and longevity.
Best Practices
- Opt for power supplies with efficiency ratings above 90% to comply with modern energy standards.
- Choose a manufacturer that offers real-time monitoring and diagnostics to track power usage.
- Work with suppliers who actively develop next-gen efficiency solutions, such as GaN (Gallium Nitride) and SiC (Silicon Carbide) semiconductors.
By prioritizing power efficiency and smart energy management, OEMs can future-proof their products and lower long-term operational costs.
7. Supply Chain Stability and Lead Time Management
Supply chain disruptions can delay production, increase costs, and impact product launches. Choosing a power supply manufacturer with stable supply chain management and optimized lead times ensures consistent availability.
Key Considerations
- Do they have multiple global manufacturing sites to prevent supply chain bottlenecks?
- Can they provide alternative sourcing for critical components in case of shortages?
- Do they offer predictive inventory management and JIT (Just-In-Time) production?
Key Features and Benefits
- Reliable product availability – Avoids production halts due to component shortages.
- Lower procurement risks – Diversified sourcing minimizes disruption risks.
- Scalable production – Ensures smooth low- to high-volume production transitions.
Best Practices
- Partner with manufacturers that have redundant supply chain strategies to mitigate unexpected disruptions.
- Work with suppliers that provide real-time inventory tracking and demand forecasting.
- Ensure the manufacturer has a logistics strategy that enables efficient global shipping and customs management.
By ensuring supply chain reliability, OEMs can reduce risks and ensure consistent delivery timelines for their power supply components.
8. Post-Sales Support, Warranty, and Technical Assistance
A power supply’s long-term reliability depends on strong post-sales support, including firmware updates, technical troubleshooting, and warranty coverage. A manufacturer that offers lifecycle support ensures product longevity and reliability.
Key Considerations
- Does the manufacturer provide dedicated technical support teams for troubleshooting?
- Do they offer firmware and software updates for programmable power supplies?
- What are the terms of their warranty policies for power supply components?
Key Features and Benefits
- Reduced downtime – Fast technical support and issue resolution.
- Extended product life – Ongoing firmware updates enhance performance.
- Lower replacement costs – Strong warranties reduce maintenance expenses.
Best Practices
- Work with a supplier that provides a structured RMA (Return Merchandise Authorization) process.
- Choose a manufacturer that offers custom support plans for high-volume OEMs.
- Ensure their technical support team is responsive to troubleshooting and maintenance needs.
A power supply partner that provides reliable post-sales support ensures long-term reliability and operational efficiency.
9. Innovation and Future-Proofing Capabilities
Technology is evolving rapidly, and power supplies must adapt to emerging industry trends such as IoT connectivity, smart power management, and high-density power conversion. A future-proof power supply ensures scalability and adaptability.
Key Considerations
- Does the manufacturer invest in next-gen power technologies, such as GaN-based high-efficiency designs?
- Are they developing IoT-enabled smart power supplies with real-time analytics and monitoring?
- Can they offer modular power solutions that support future product enhancements?
Key Features and Benefits
- Scalable technology – Power supplies can be upgraded without complete redesigns.
- IoT-ready solutions – Enables remote diagnostics and predictive maintenance.
- Next-gen efficiency – Uses advanced semiconductors for higher power density.
Best Practices
- Choose a manufacturer actively investing in R&D for next-gen power solutions.
- Opt for power supplies that support adaptive voltage scaling and real-time load balancing.
- Ensure that your partner can customize solutions to support future product innovations.
Working with an innovative power supply partner helps OEMs stay ahead of industry trends and regulatory requirements.
10. Why Phihong is the Ideal Custom Power Supply Partner for OEMs
Choosing the right custom power supply manufacturer is essential for OEMs looking for reliability, scalability, and efficiency. A trusted supplier must offer cutting-edge engineering, compliance assurance, and supply chain stability.
Why Choose Phihong?
With over 50 years of experience, Phihong is a globally recognized custom power supply manufacturer, specializing in tailored power solutions for industrial automation, medical applications, telecom, and EV charging.
Key Benefits of Partnering with Phihong
- Custom engineering and scalable production – Phihong offers high-efficiency AC-DC and DC-DC power supplies designed to meet OEM-specific needs.
- Certified power solutions – Phihong’s power supplies comply with UL, IEC, MIL-STD, and RoHS for seamless global deployment.
- Supply chain resilience – Manufacturing facilities in Vietnam ensure consistent availability and flexible production scaling.
- Advanced PoE and energy-efficient designs – Phihong leads in high-wattage PoE power supplies, supporting smart networks and industrial automation.
- Comprehensive lifecycle support – From design to post-production, Phihong offers firmware updates, long-term product availability, and RMA services.
For OEMs seeking a reliable power supply partner, Phihong delivers high-quality, compliant, and future-proof solutions that optimize efficiency and product integration.
If your business requires custom power supply solutions tailored to your needs, explore Phihong’s capabilities today to find the right OEM power supply solution for your applications.
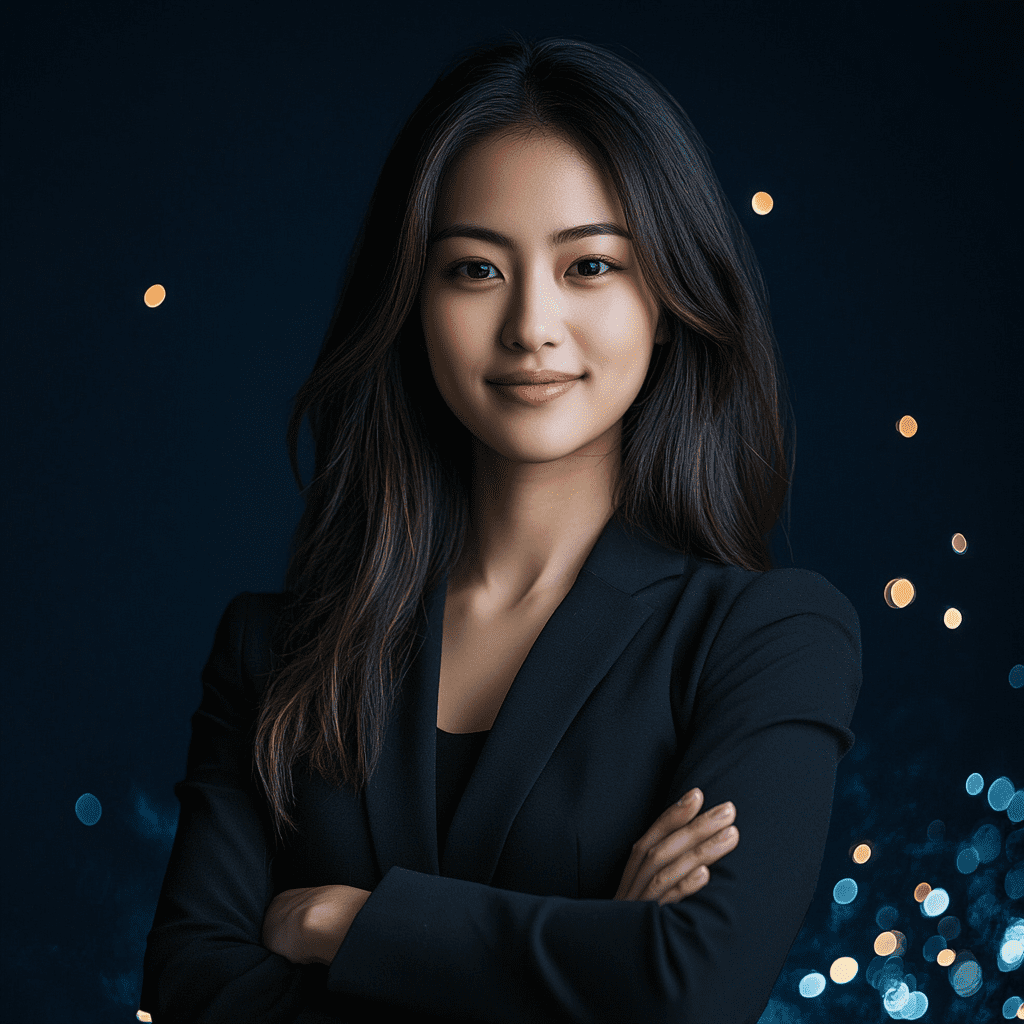
Contact Our Team Today!
Our dedicated sales team and international partners are prepared to support you with your latest projects and initiatives globally.
Explore More with Phihong USA
As we conclude our exploration of PoE technology, it’s evident how these innovations are streamlining power and data integration across various industries. Phihong USA stands at the forefront of this technological advancement, offering a diverse range of power solutions designed to meet the evolving needs of modern industries.
Phihong USA’s extensive product lineup includes:
- Power over Ethernet (PoE) Solutions: Delivering reliable power and data transmission over a single cable, ideal for simplifying network installations and reducing costs.
- AC/DC Adapters and Power Supplies: From compact adapters to industrial-grade power supplies, Phihong provides solutions that ensure efficiency and reliability in various applications.
- Battery Chargers: Customizable chargers for lithium-ion and lead-acid batteries, supporting a wide range of power requirements for mobility and industrial applications.
- Medical Power Supplies: Specialized power solutions designed to meet the stringent requirements of the healthcare industry, ensuring safety and reliability.
Phihong USA is committed to innovation and excellence, continually developing products that meet the highest standards of performance and reliability. Their global reach and dedication to customer support make them a trusted partner in powering the future.
Here are some useful links to explore Phihong USA’s offerings further and bring in new potential clients:
Visit Phihong USA to discover how their advanced power solutions can support your business needs. Whether you’re looking to upgrade your network, or find reliable power supplies, Phihong USA has you covered.
By choosing Phihong USA, you’re partnering with a leader in power technology, ensuring your operations run smoothly and efficiently with top-tier power solutions. Contact Us today!
FAQ
What are the key benefits of working with a custom power supply manufacturer instead of using off-the-shelf solutions?
Working with a custom power supply manufacturer provides OEMs and industrial manufacturers with several advantages over using off-the-shelf solutions. The most significant benefit is tailored performance, as custom power supplies are engineered to meet precise voltage, power efficiency, and regulatory requirements that generic power supplies may not accommodate.
Custom solutions also enhance product reliability, ensuring that power supplies integrate seamlessly with the OEM’s equipment while reducing the risk of electrical failures or overheating issues. This is particularly crucial for medical, telecom, industrial automation, and EV applications, where stable and precise power delivery is essential for safety and efficiency.
Another major advantage is compliance with industry-specific regulations. Custom power supplies are designed to meet UL, CE, IEC 60601 (for medical devices), MIL-STD-810 (for aerospace/defense), and RoHS compliance. Off-the-shelf power supplies may not always meet these strict standards, increasing the risk of regulatory issues or market restrictions.
Customization also allows for flexible design options, including form factor modifications, custom enclosure designs, and advanced cooling solutions. This ensures that the power supply fits within space-constrained or ruggedized applications without performance loss.
Finally, custom power supply manufacturers provide lifecycle support, offering firmware updates, scalability options, and long-term availability, whereas off-the-shelf solutions might become obsolete quickly. OEMs investing in custom power supplies ensure a stable, long-term solution, reducing the risk of redesigns due to discontinued components.
How do I determine the best power efficiency level for my custom power supply?
Selecting the right efficiency level for a custom power supply depends on the application, power consumption needs, and regulatory requirements. Higher efficiency reduces wasted energy, minimizes heat generation, and improves device longevity, making it a critical factor in power supply design.
Power efficiency is measured in percentages, with most modern power supplies targeting efficiency ratings of 85% to 98%. For industrial and telecom applications, ENERGY STAR® and 80 PLUS® certifications are recommended to ensure low power loss and minimal heat output. For medical and aerospace applications, high-efficiency power supplies ensure consistent performance in critical environments.
To determine the right efficiency level:
- Calculate your load requirements – A higher load demand requires a power supply with optimized power factor correction (PFC) to reduce energy losses.
- Consider regulatory mandates – If your product is sold in multiple regions, ensure compliance with DOE Level VI (U.S.), EU CoC Tier 2, and IEC 62368-1 energy efficiency regulations.
- Assess cooling requirements – A high-efficiency power supply generates less heat, reducing the need for complex cooling systems and improving overall reliability.
- Look for next-gen technologies – GaN (Gallium Nitride) and SiC (Silicon Carbide) semiconductors provide higher power density and efficiency gains over traditional silicon-based solutions.
Working with a custom power supply manufacturer ensures that your power solution meets energy efficiency goals while balancing thermal performance and regulatory compliance.
What factors should OEMs consider when choosing between AC-DC and DC-DC power supplies?
OEMs must evaluate several key factors when deciding between AC-DC and DC-DC power supplies, as each serves distinct applications and power conversion needs. AC-DC power supplies convert alternating current (AC) from a power source into direct current (DC) needed by electronic devices, making them ideal for commercial, industrial, and medical equipment that plugs into wall outlets. DC-DC converters, on the other hand, are used to step up or step down DC voltage levels, making them essential for battery-powered devices, electric vehicles, and portable electronics.
Key Considerations for AC-DC Power Supplies:
- Use Case – Required for applications that draw power from the grid or an AC generator.
- Voltage Stability – Designed to maintain consistent voltage levels regardless of input fluctuations.
- Regulatory Compliance – Must meet safety and electromagnetic interference (EMI) regulations, such as IEC 60950, UL 62368-1, and Energy Efficiency Directives.
Key Considerations for DC-DC Power Supplies:
- Portability – Used in battery-powered devices, automotive electronics, and aerospace systems where DC voltage regulation is needed.
- Size and Weight – Smaller form factors allow for compact, lightweight power solutions.
- High Efficiency – DC-DC converters can achieve efficiency levels above 95%, reducing energy waste and heat generation.
OEMs selecting a custom power supply manufacturer should confirm that they offer both AC-DC and DC-DC options, ensuring seamless integration with device power requirements.
How does thermal management impact power supply performance and longevity?
Effective thermal management is critical to ensuring a custom power supply operates efficiently while maintaining reliability and longevity. Excessive heat can cause power inefficiencies, shorten component lifespan, and increase system failures, making heat dissipation strategies essential in power supply design.
Key Thermal Management Strategies:
- Passive Cooling – Heat sinks, thermal pads, and optimized PCB layouts dissipate heat naturally without moving parts.
- Active Cooling – Forced air via fans or liquid cooling systems improves thermal regulation in high-power applications.
- Phase-Change Cooling – Advanced heat pipe technology transfers heat away from critical components, ensuring consistent power performance.
Why Thermal Management Matters:
- Prevents Overheating – Protects components from thermal stress and premature degradation.
- Improves Efficiency – Well-managed heat dissipation reduces energy loss and maintains high power conversion efficiency.
- Extends Product Lifespan – A properly cooled power supply experiences fewer failures and longer service life.
Choosing a custom power supply partner that offers advanced thermal management solutions, such as integrated heat dissipation designs and optimized airflow systems, ensures higher reliability and longer operational life for power solutions.
What industries benefit the most from custom power supply solutions?
Custom power supplies provide tailored energy solutions for a wide range of industries, ensuring optimized performance, safety, and efficiency. Industries that benefit most from custom power solutions include:
1. Medical & Healthcare
- Medical imaging, ventilators, and patient monitoring devices require low-noise, highly regulated power supplies compliant with IEC 60601 safety standards.
2. Industrial Automation & Robotics
- Factory automation, PLC controllers, robotic arms, and conveyor systems rely on ruggedized, high-efficiency power supplies with wide input voltage support.
3. Telecommunications & Networking
- 5G base stations, network switches, and fiber-optic systems need PoE power solutions with remote power monitoring capabilities.
4. Aerospace & Defense
- Military-grade power supplies meet MIL-STD-810 compliance for use in avionics, satellite communication, and mission-critical defense applications.
5. Electric Vehicles & Renewable Energy
- EV charging stations, battery management systems, and solar inverters require custom DC-DC and bidirectional AC-DC converters to support energy storage and power distribution.
Partnering with an experienced custom power supply manufacturer ensures OEMs in these industries receive reliable, compliant, and efficient power solutions tailored to their specific needs.